Case Study: Optimization Through Digitalization for the Novolyze Platform
There are many ways to optimize organizational efficiency, one of which is streamlining internal processes. This is particularly crucial in food safety and quality related processes, where high standards are essential, and any mistake can slow down or even halt food production temporarily. Continue reading to see how, by working closely with Novolyze, a French company, we helped their clients save an average of 2 hours per task through the digitization of processes.
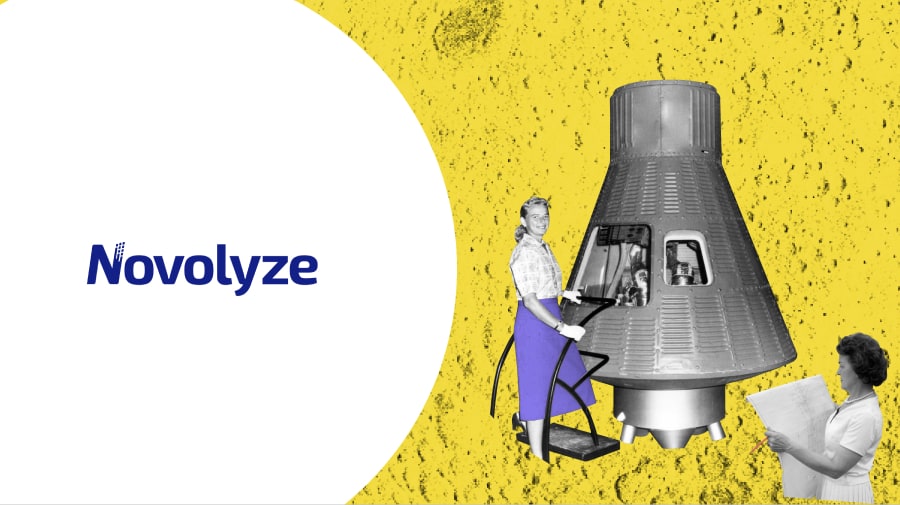
Table of contents
The Client
Novolyze is a Food Safety company. The company offers solutions to help the food industry manufacture safer food, while ensuring strong compliance with international Food Safety & Quality standards. Their research work mainly focuses on evaluating the inactivation of foodborne pathogens under various kinds of stress (heat, etc.). Based on this expertise, Novolyze has developed the first range of dried, ready-to-use surrogate bacteria, an innovation that allows the food industry to test the efficacy of microbial kill steps/intervention steps in real-life conditions. Novolyze relies on state-of-the-art infrastructures, installed in a pharmaceutical-grade environment at their R&D Center in Dijon, France.
Their product is a SaaS, a food quality management platform that offers customizable dashboards, streamlined reporting, trend analysis, and ensures timely delivery of products with the correct specifications. It notifies when the deviations occur and ensures that all products leave the facility on-time and with the right specifications.
The Challenge
Our partnership with Novolyze began in 2020 when they looked for a technological solution to optimize production process control, aiming to enhance efficiency in both time and cost. They needed solutions that would help to digitize processes for better cost and time efficiency and improve their efforts in acquiring new customers and expanding their audience.
Why Boldare?
Novolyze appreciated our actions and lean startup approach, previous experience with prototypes and MVPs. In addition they appreciated our UX/UI skills and experience of our experts.
The Collaboration Overview
Like with many other collaborations, we started working with the client on a smaller product, so the Novolyze team could experience our services in practice. The first product we created was a prototype of one of the features client wanted to implement into their platform.
Small scrum team consisted of a Product Designer and a Scrum Master, and the process took two weeks. We kicked-off work with a workshop that aimed to meet Novolyze’s needs. The idea was to create a prototype of a new feature and validate the idea and collect feedback from the marketing team and potential leads. After positive validation and feedback, the client wanted to continue collaboration with our team and work on Minimum Viable Product.
We consequently worked on Novolyze’s products, helping the company to adjust their product to the market demand. During 3 years we delivered:
- A cross functional scrum team of Front End Developer, Product Designer and Scrum Master to develop Novolye’s main products
- DevOps support on demand
- Quality Assurance Engineer support with test automation
- Scrum trainings
- Product Strategist consultations
Product insights
Through three years of collaboration we contributed to the development of Novolyze’s key product and its modules designed for various needs of their clients: Process Control, Sanitation Control and Environmental Monitoring.
The primary challenge for us was the absence of a benchmark or existing market solution that could address the complex needs of maintaining hygiene and cleanliness in the food production lines. The requirements were to create a system that not only facilitated the cleaning of equipment and maintained the cleanliness of production areas but also integrated workplace sanitation protocols into a structured agenda for cleaning activities. This included a human-centered approach with checklists and standard operating procedures that could be universally applied across the company’s global operations. The platform was designed by Boldare’s Product Designer from scratch, according to Novolyze requirements and data.
The core of the platform encompasses all activities occurring within the factory premises. This tool enables the maintenance of global standards of cleanliness and hygiene through continuous monitoring, analysis, tickets and actions management, and process control. Thanks to the tool, Novolyze’s clients can maintain the same standards in all food production lines in factories across the globe.
The Novolyze solution offers customization to align with the unique needs and plans of each client. Its adaptability across various operational scales and global locations ensures the consistent application of stringent safety and security standards.
Here’s a potential use case of Novolyze’s platform: clients can use the platform to prepare a production line that previously processed nut-based food products in such a way that it can begin producing another product without concerns about the presence of allergenic nuts in the new product prepared on that line. Thanks to the standardization of processes offered to users via the Novolyze platform, the production preparation process can be shortened by up to 2 hours.
UX/UI Design Process
To meet Novolyze needs, we conducted thorough research and user interviews. We guided them through user journeys, jobs-to-be-done, clickable demos, personas, mock-ups, and more. We played multiple roles as contributors, collaborators, and strategists.
The best evidence of customer satisfaction are the references given to our UX designer, Łukasz, by one of the product stakeholders:
Łukasz helped us make something from nothing. As a member of my UX team we created a new product for both our company, as well as our industry. He guided us through user journeys, jobs-to-be-done, clickable demos, personas, UIs and much more. He acted as a contributor, collaborator, and strategist. I recommend adding Lukasz to your team, and I look forward to working with Łukasz again in the future.
Technology Stack
We utilized .NET for the backend and Angular for the frontend.
We started our partnership with a prototype, delivered MVP and helped to achieve the Product Market Fit phase.
Conclusion
Our collaboration is a great example of how the digitization of processes can improve companies’ and clients’ businesses. Together, we created a platform for faster detection of food contamination, streamlining Novolyze’s business and enabling them to deliver high-quality services and strengthen their market position as a leader and innovator.
Share this article: